A unique piece that puts art and science on the same wavelength
The Lambda Ring
The Process
Lambda 1
The Lambda Ring was crafted to embody the values of connection and synchronization. Based upon the Greek letter used in physics for wavelength, the lambda (λ) encourages the wearer to be “on the same wavelength” as their friends, family, partner, or best self.
To create the first iteration, Lambda 1, I had to broaden my ways of thinking. Throughout the process, I learned stylistic solid modeling, mold making, and casting methods. Simultaneously, I had to build upon my knowledge of materials and fabrication to develop the ring to be durable, comfortable, and beautiful.
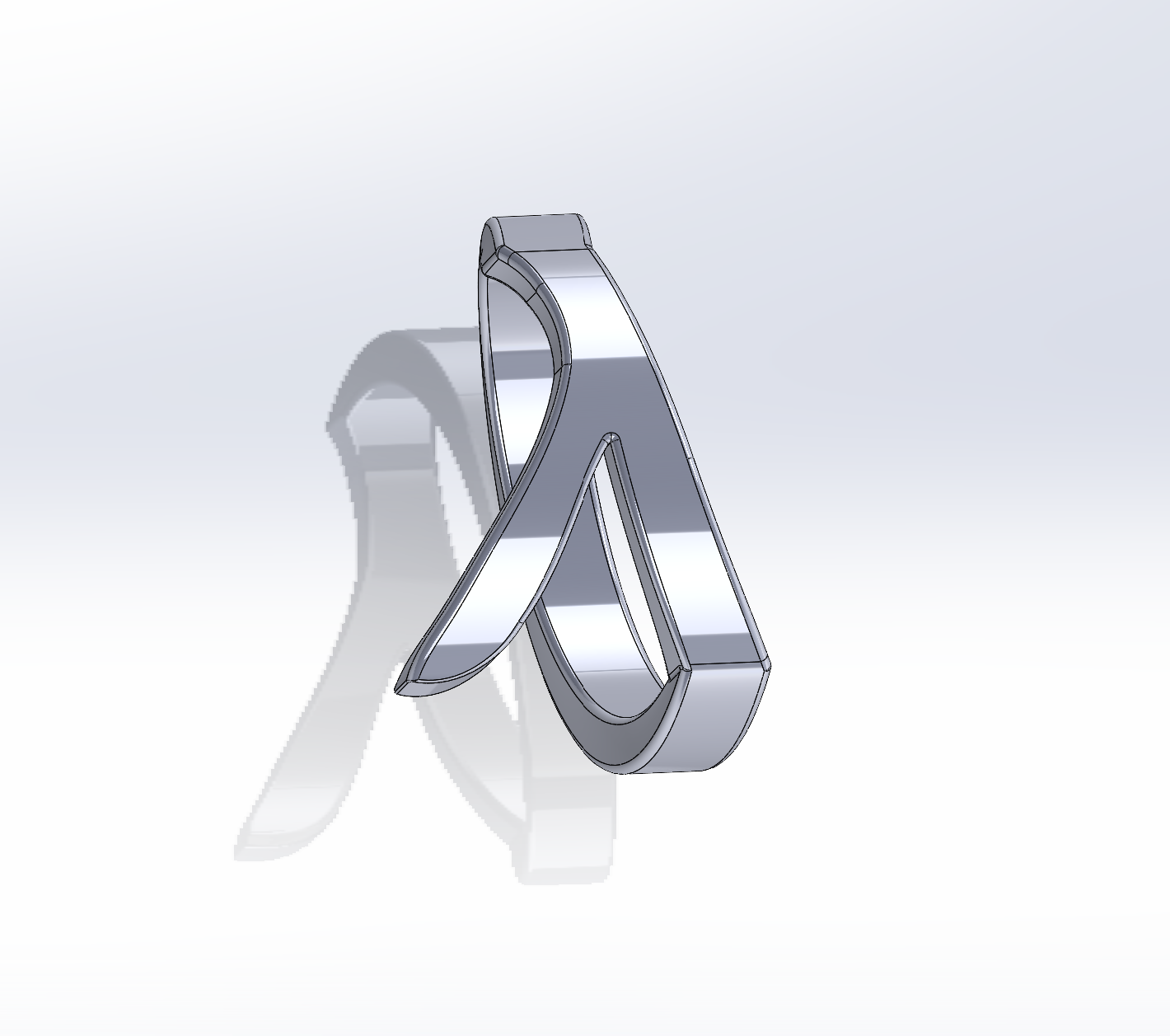
First, I created a CAD model in Solidworks to 3D print resin masters from
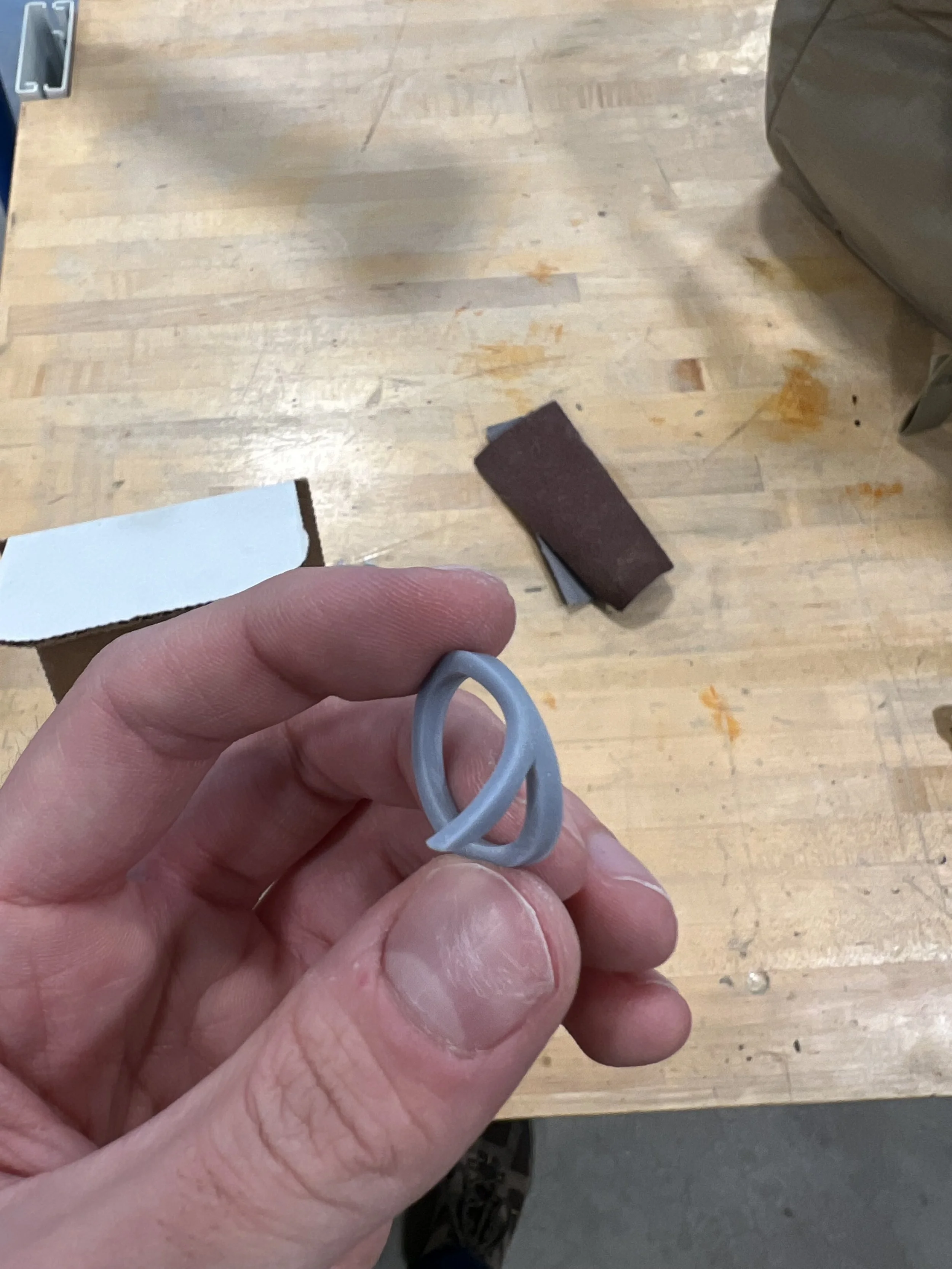
Master made in UV resin with stereolithography 3D printing
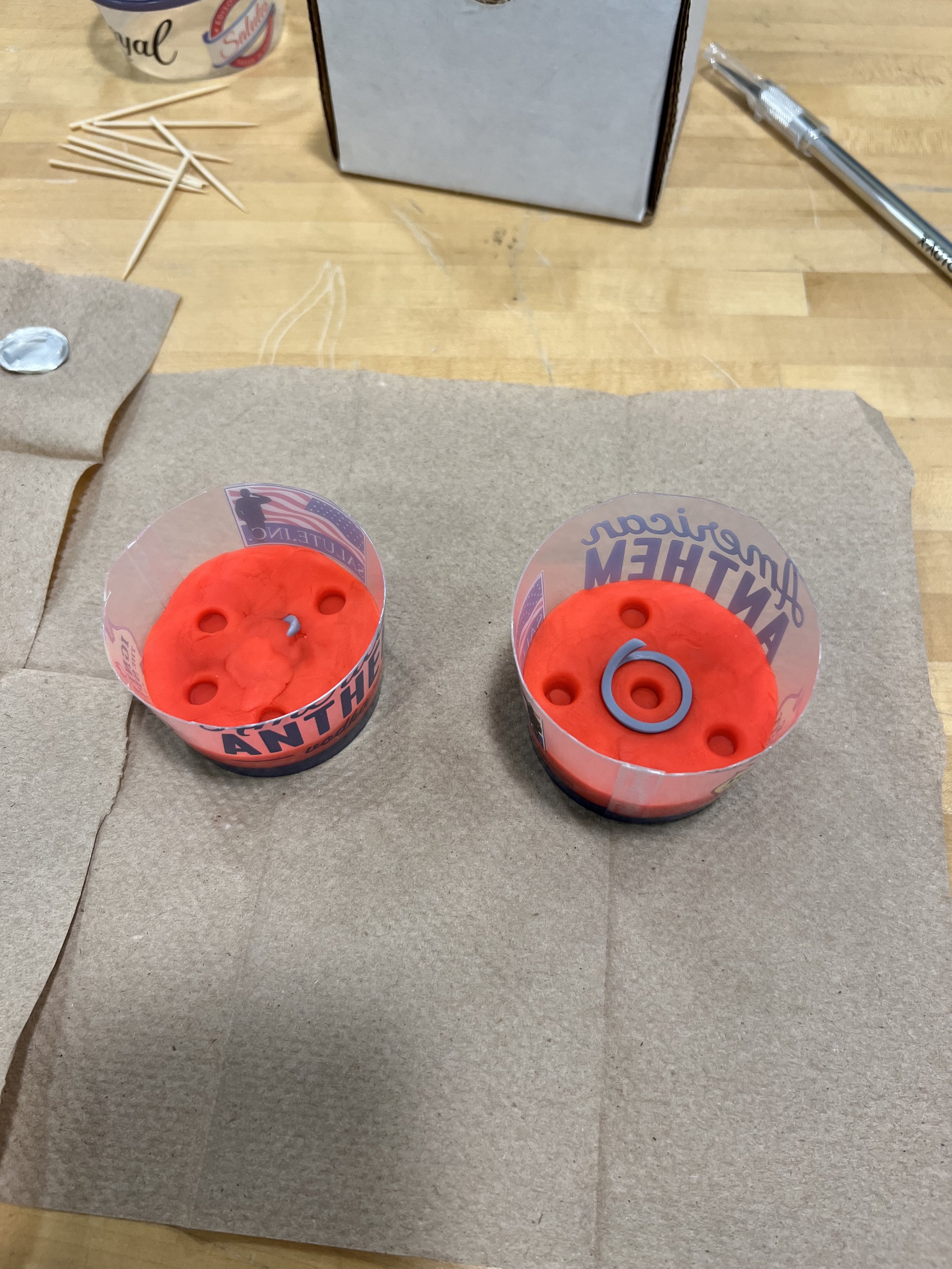
Two molds encasing different sizes of rings in Play-Doh in order to make half the mold
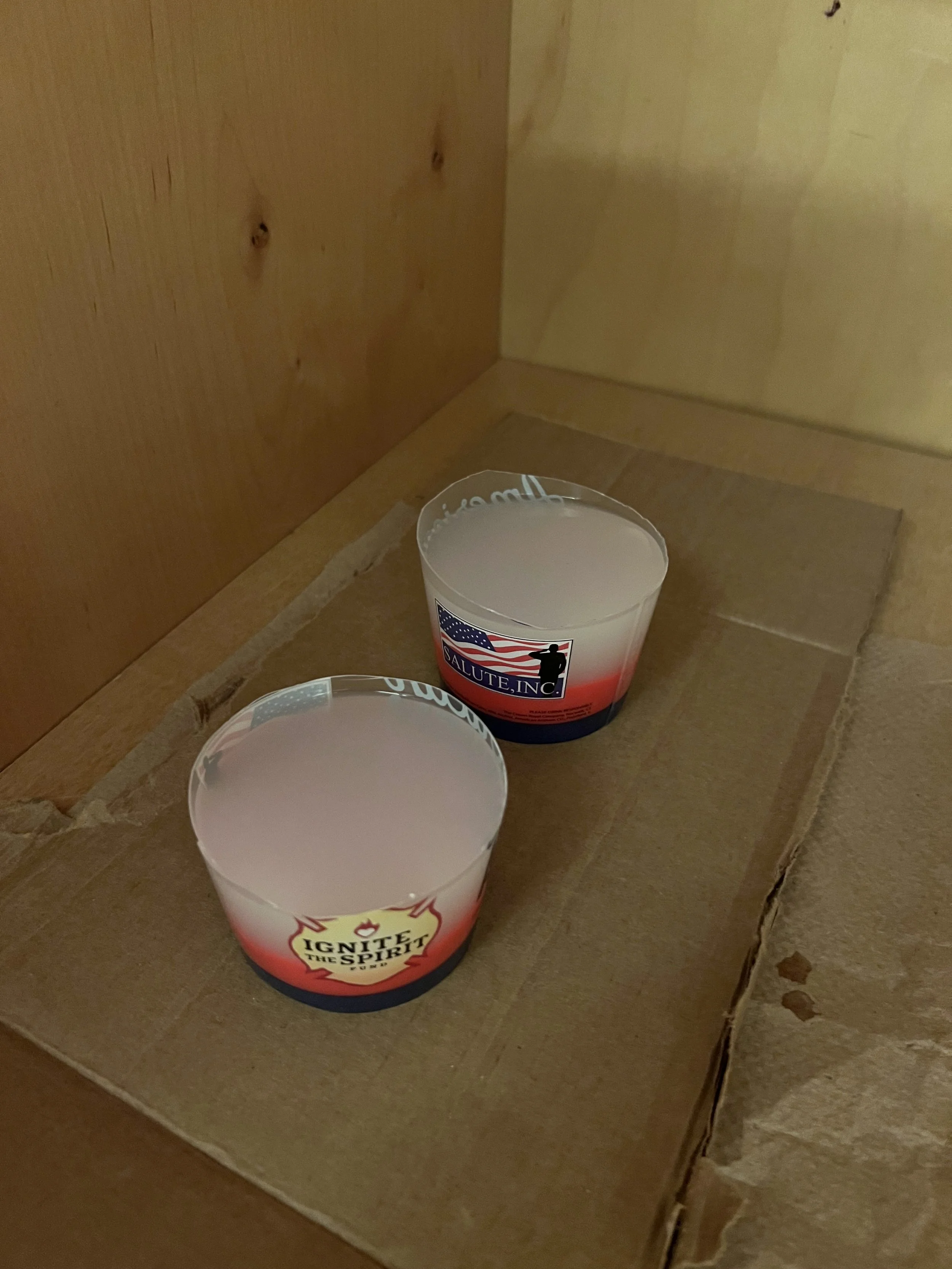
Half the mold poured with silicone

Finished molds injected with green-dyed epoxy resin
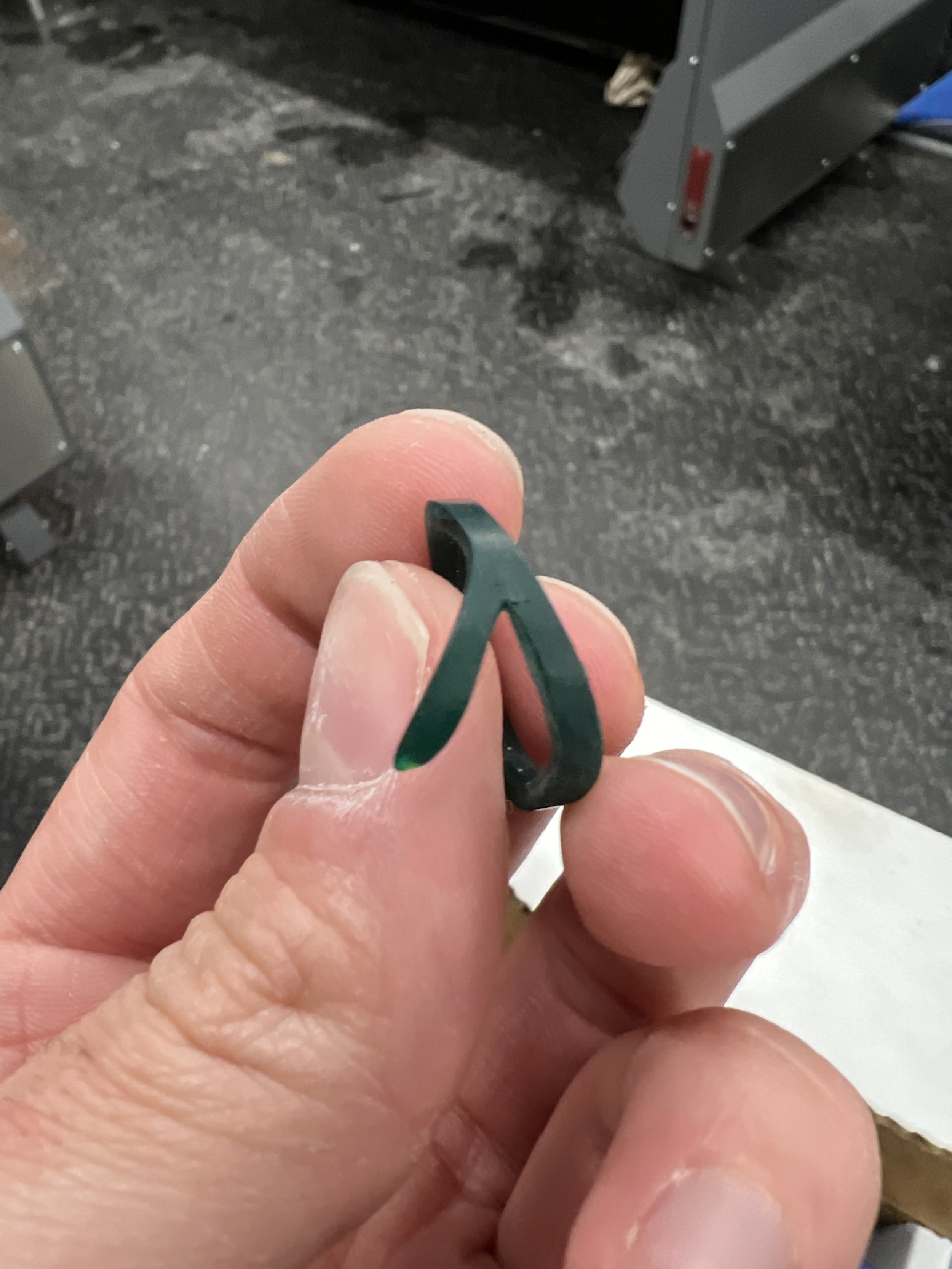
Finished ring!
Lambda 2
The Lambda 2 ring was created to solve molding problems discovered in Lambda 1. From the first iteration of the Lambda Ring, I learned many skills and ways to improve the design. While I had previous experience in 3D printing, I had never used the stereolithography (SLA) process before. This type of 3D printing gave me a very high-fidelity and precision model, however, due to the properties of the resin, the silicone was inhibited from curing properly. To remedy this, I spray-painted the next iteration master with primer before molding. Additionally, my first molds did not allow for air bubbles to escape. In the Lambda 2 prototype, I added vent tubes to eliminate voids.

3D printed master with vents to eliminate bubbles

Master spray painted to stop cure inhibition and sticky molds
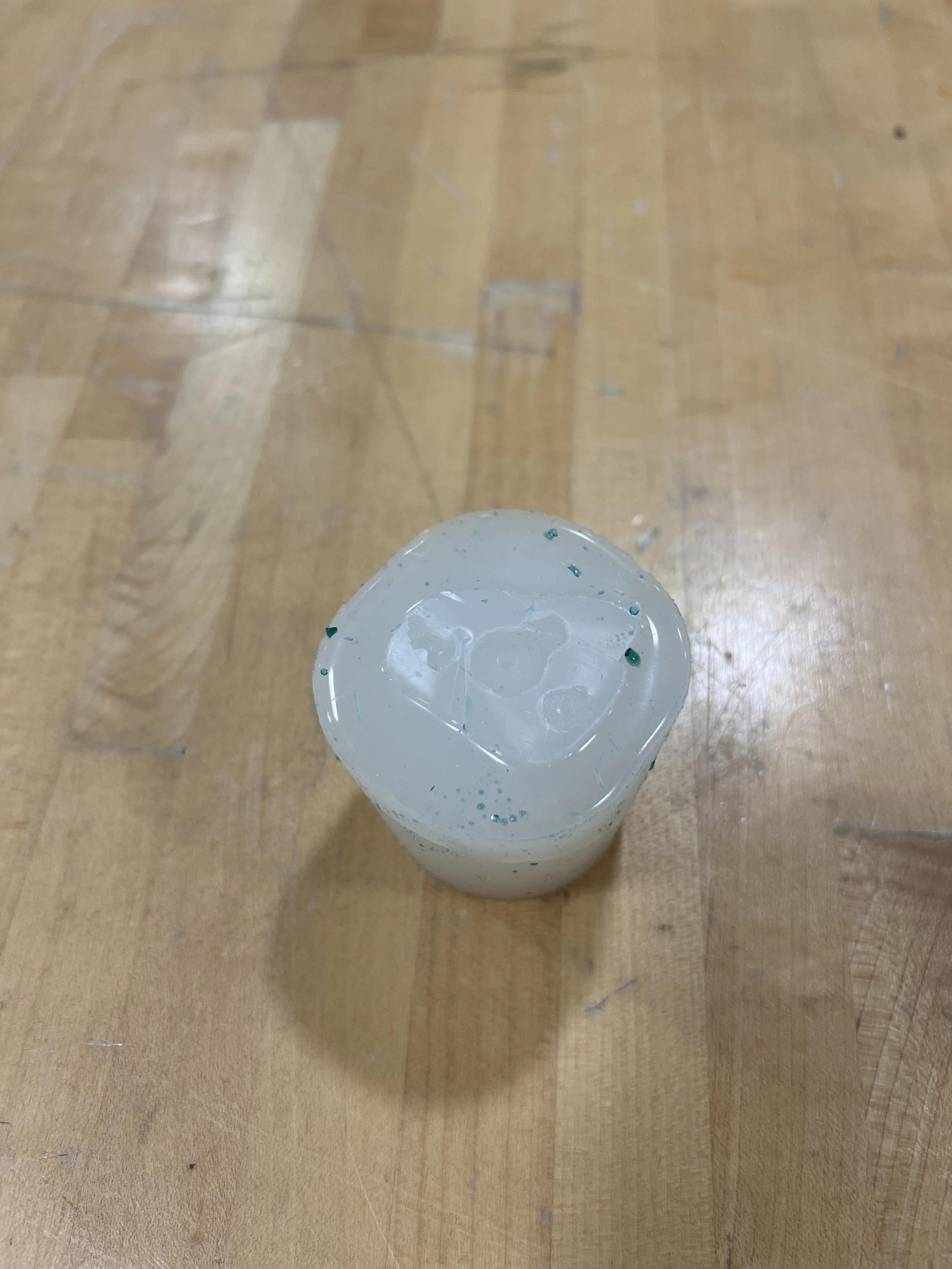
Finished mold showing vent holes

Mold halves created by cutting master out of silicone cylinder
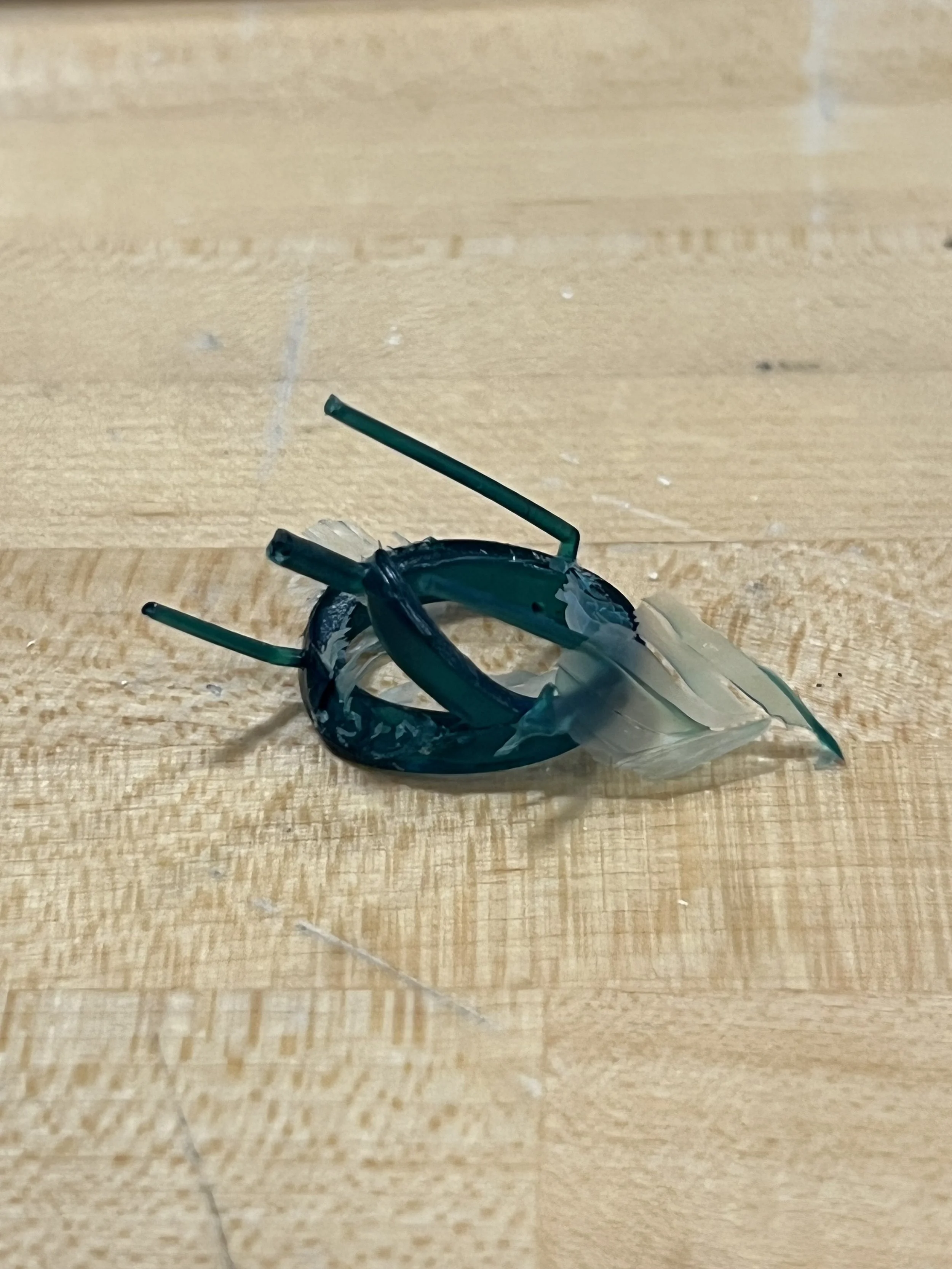
Cast ring showing minimal bubbles!
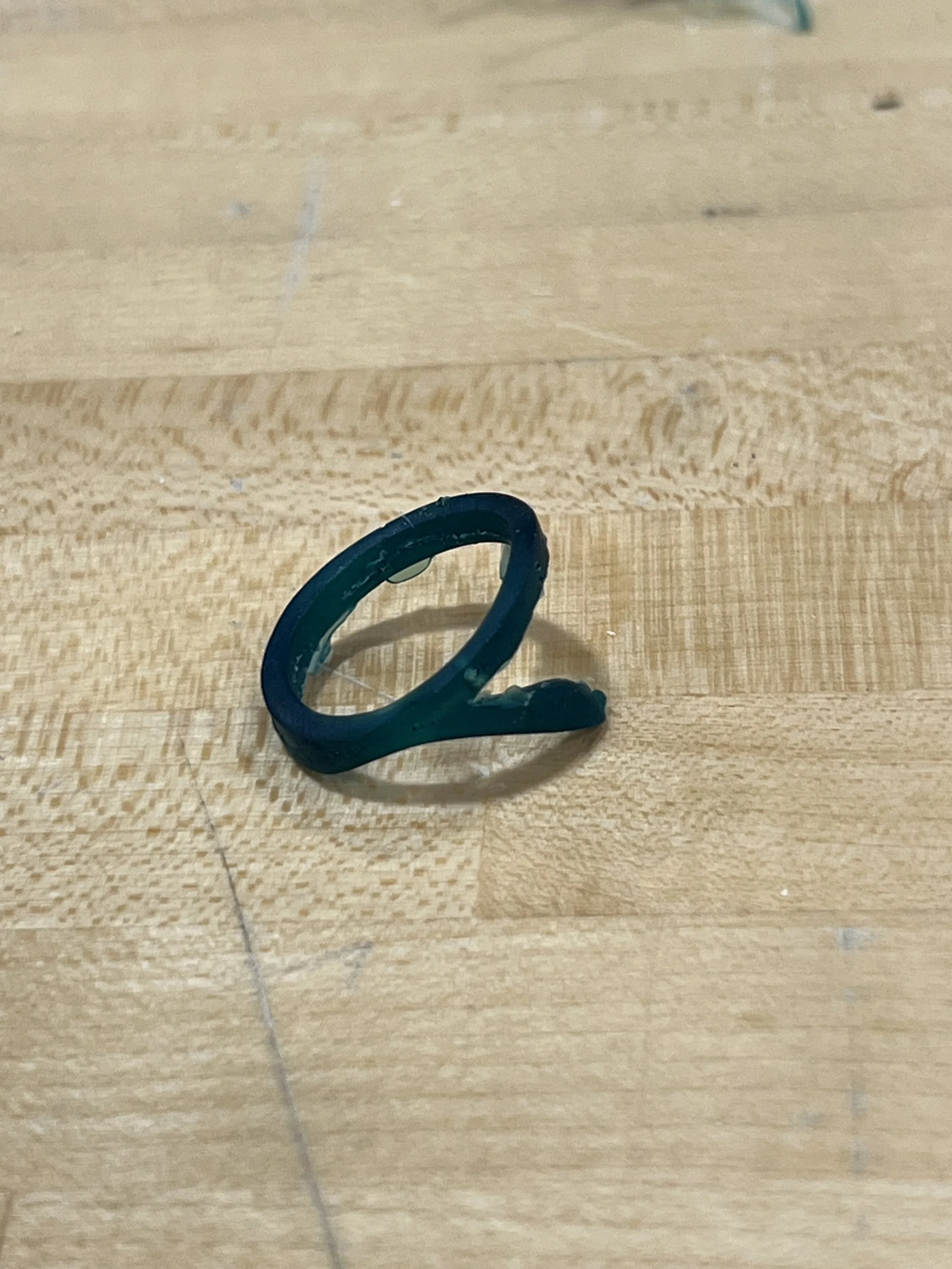
Flashing is cut off to begin finishing
Lambda 3
While the Lambda 2 prototype marked a vast improvement in casting quality, it lacked strength while being worn: the Lambda 3 ring solves this problem. Both the Lambda 1 and Lambda 2 versions regularly broke during use, typically around the lambda’s arm or the sharp corners where the symbol blends into the band. By learning how to model with surfaces in Solidworks, I eliminated the sharp corners and stress concentrators within the ring. The Lambda 3 prototype was also cast using different materials such as urethane resin and sterling silver. Having a higher modulus of elasticity than epoxy, urethane is more ductile and handles impacts better than the brittle epoxy, but it is molded in the same way. Similarly, sterling silver is commonly used in jewelry for its ductility and shiny appearance. To make the ring out of silver, I outsourced it to be investment cast and finished the raw castings by hand.
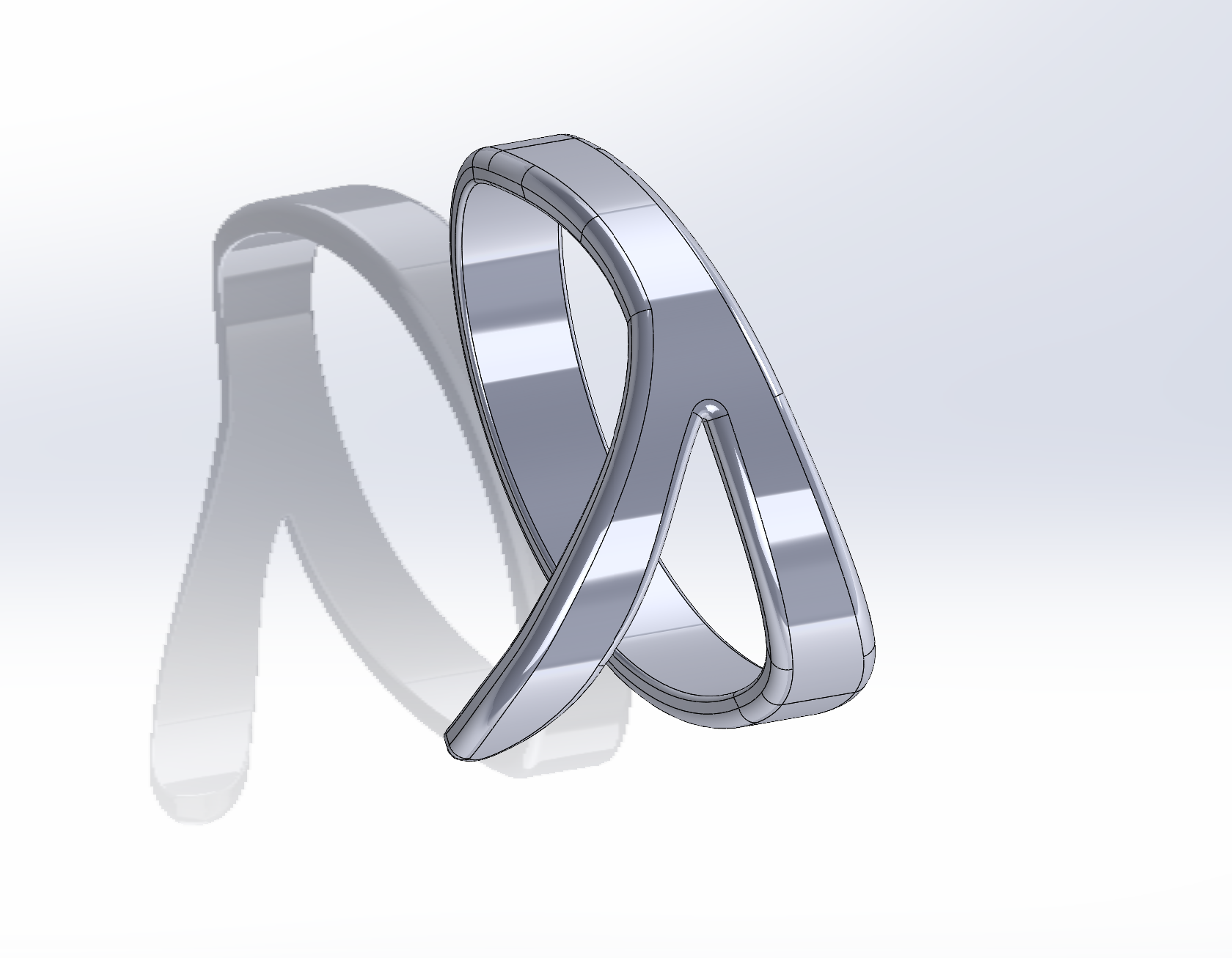
Lambda 3 CAD showing smoother corners with less stress concentration

Three sizes of rings cast in urethane resin
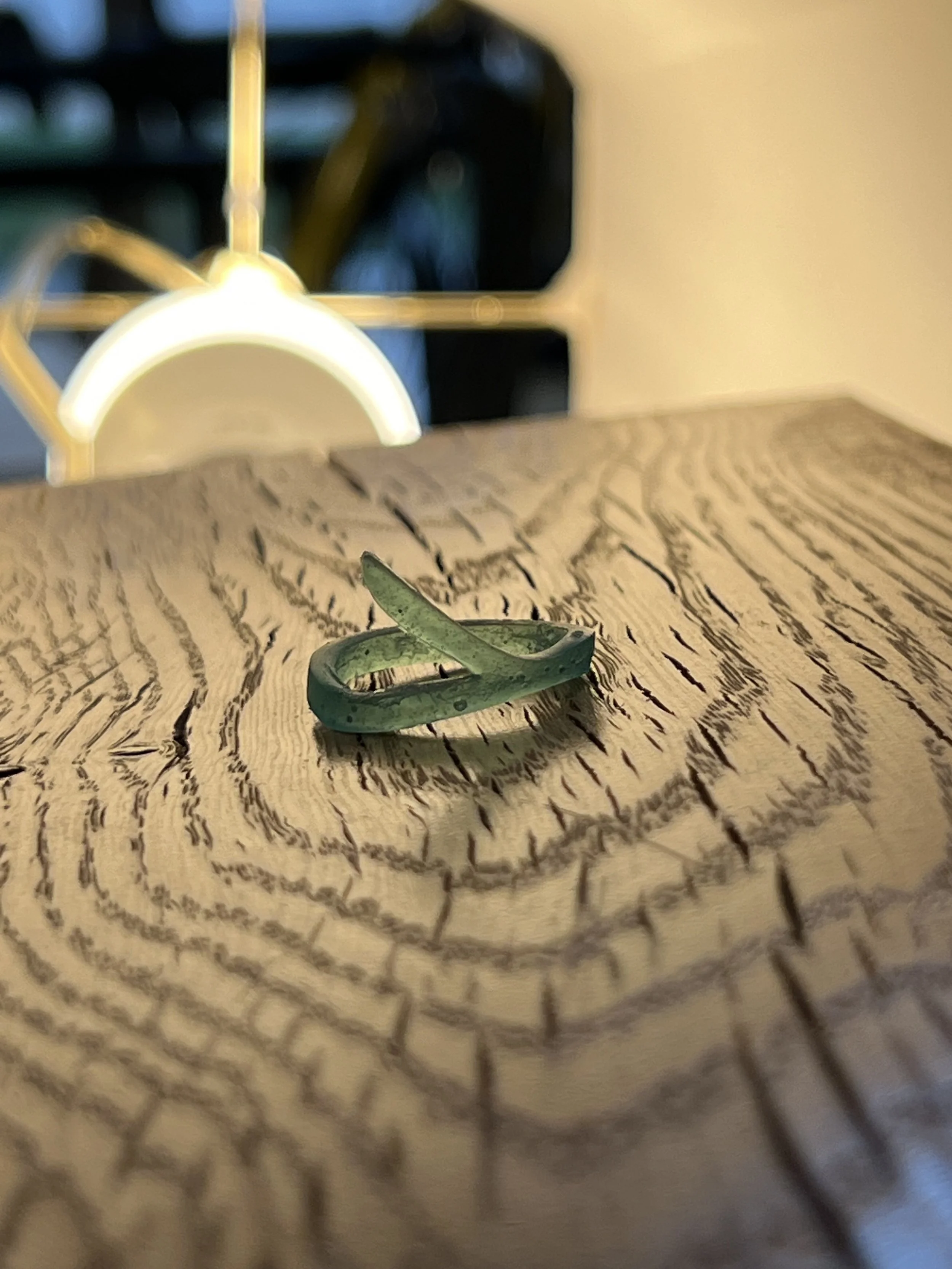
Matte finishing makes the ring translucent
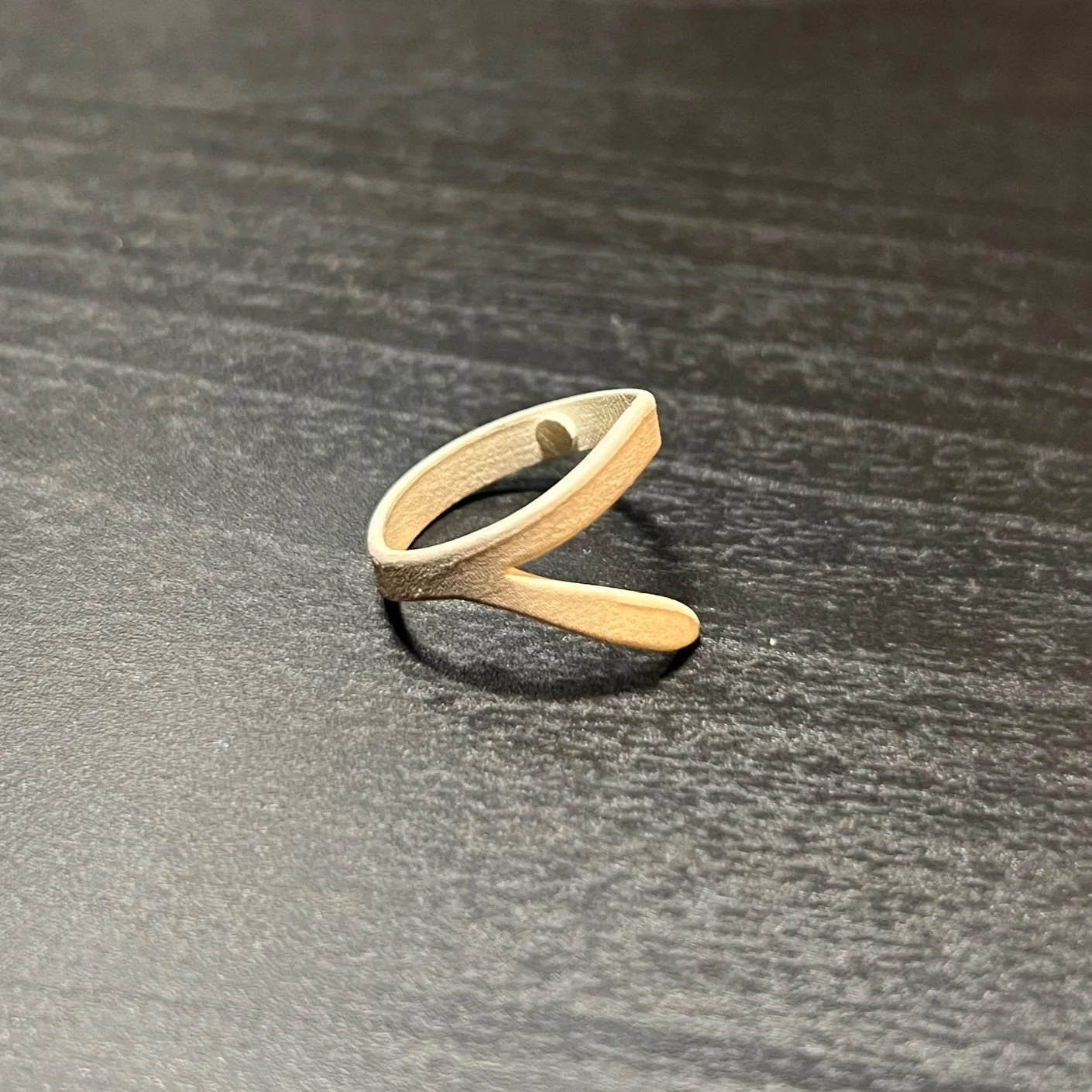
Unfinished ring made by the lost-wax method
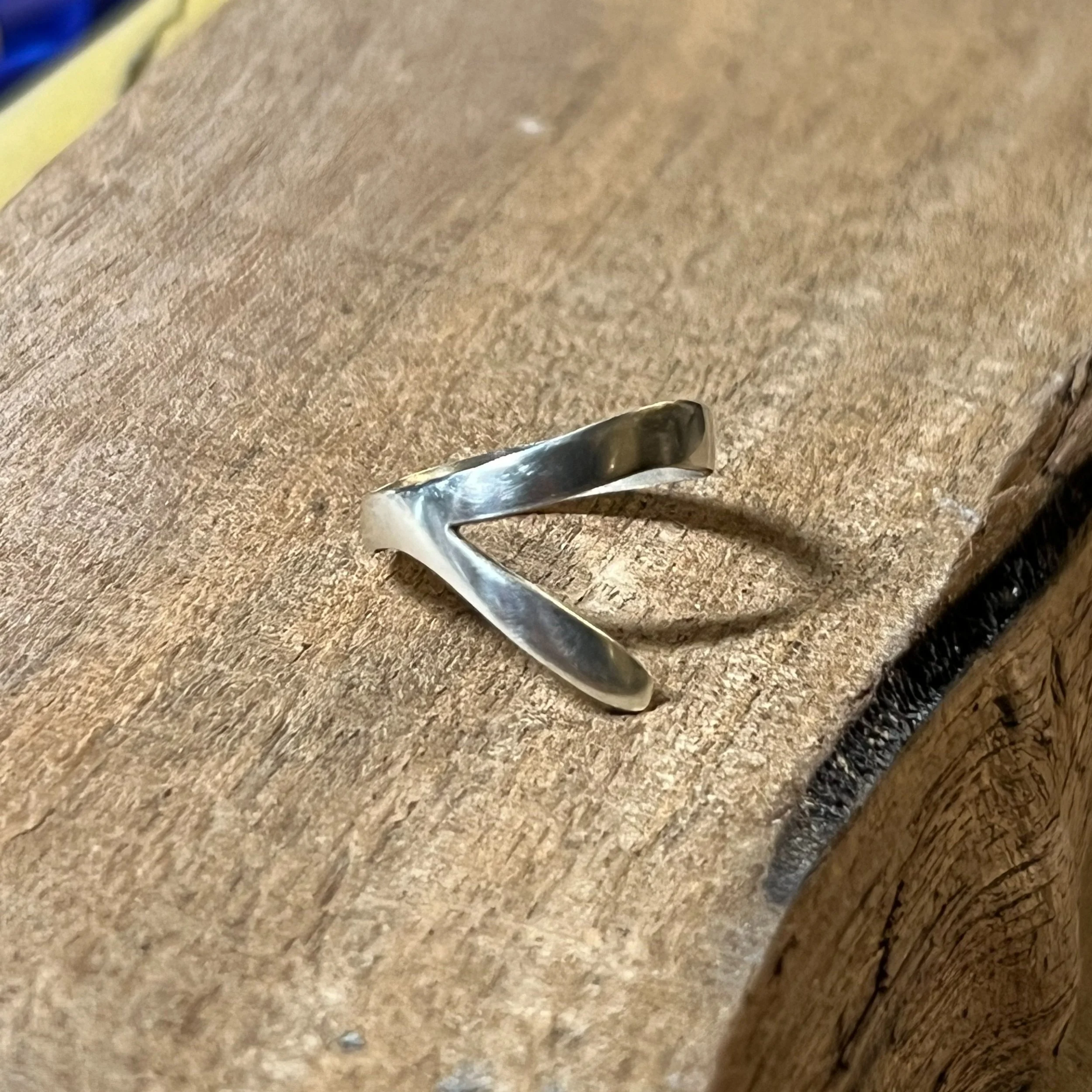
Finished and polished Lambda 3 Silver

Lambda 3 Resin being worn